点击【 大 中 小 】, 可 以 选 择 字 体的大小,以便 你 阅读.
1 引言
莱钢新建3#750高炉槽下称量系统中采用现场总线技术,通过Schneider公司的智能称重模块和MB+网络软、硬件构成现场实时数据采集网,实现测量数据的数字化传输,提高了入炉炉料重量信号的测量精度和测量系统的抗干扰能力。较好解决了现场一次测量装置所采集的信号在传输过程中受到干扰影响而产生畸变和失真的问题。
2槽下配料工艺概况
高炉入炉炉料包括大烧结矿、小烧结矿、焦炭、烧结球团及其它辅料,分别从原料场、竖炉和烧结机运来,经槽上输送到各个料仓。根据入炉料单来选择炉料的种类和重量,选中一个料仓时,仓内炉料经振筛输送到称量斗称量,称量后经皮带去上料小车,送到炉顶料罐。示意图如图1所示:
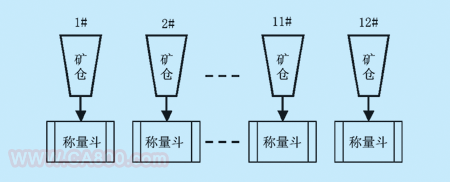
图1 工艺流程示意图
3 智能称量系统的拓朴结构
智能称量系统的现场总线以MB+网和12个ISP Momentum Weighing Module为主干,构成令牌总线,通过槽下PLC的NOM模块与控制系统相联。PLC控制器通过NOE以太网模块接入3#750高炉光纤主干网(以太网),服务器与工作站均接在以太网上,如图2所示。

图2 智能称量系统的拓扑结构示意图
12个ISP Momentum Weighing Module按逻辑环的顺序依次持有令牌,谁得到令牌,便有权与控制器交换信息,包括控制指令、采集的数据、奇偶校验、模块状态等。有效的重量信号则由控制器转发到服务器,由控制器和工作站共享,控制器利用这些信号进行实时配料控制,进行料空、料满判别,炉料水分补正,炉料配比控制等,并在工作站的监控画面上显示。
4 智能称量系统的软件功能
该系统的软件功能包括通讯、称量装置设定与校验、智能控制、历史记录与打印设置等。
4.1 通讯功能
为适应不同应用场合,系统预留多种通讯方式和接口,通讯接口有:用于网络通讯的MB+、MB、MBTCP/IP、M1;作为现场编程接口的RS232/RJ11,它可在现场组态或单个模块独立运行;作为现场显示端口的RS485/RJ11;一个作为现场打印口的9PIN串口。该系统基于现场总线技术,通过MB+口数据上传到服务器,其它接口则作为应急备用。
该系统基于MB+网,12个智能模块组成逻辑令牌环,每个模块依次获得令牌,当第i个模块得到令牌时,便有权与控制器交换信息,包括控制指令、采集的数据、奇偶校验、模块状态等。有效重量信号则由控制器转发到服务器,该模块完成后,便将令牌传给另一个模块,如此循环下去。若某一个模块出现故障,则将其从逻辑环中自动清除,待其恢复后再接入逻辑环中。现场总线的通讯速率为1Mbps。
4.2 称量装置设定与校验
(1) 称量装置设定
l 称量间隔:为适应不同大小的称量斗和不同的物料,要进行称量间隔设定,间隔的等级从0.01、0.02、0.05、0.1 ……最大到50000kg,用户要根据称的额定值来选择相应的称量刻度;
l 称量极限设置:系统给出三个选择:2%MR、5%MR、9%MR(Max Range),可根据设备的状态灵活选择。
(2) 称量装置校验:称量装置校验分三种模式,两个阶段。
三种模式:
·标准模式:当校称载荷≥75%MR时,按此模式校称;
·降级模式:当校称载荷达不到标准模式要求时,执行此模式;
·强制模式:当认为上次校称有问题或无效时,执行此模式覆盖上次的校验,该模式又分增荷和降荷两种。
两个阶段:
·零点校验:称量斗为空,根据各称量斗的自重来调节称的零点;
·载荷校验:用适当的载荷来标定称量装置的线性度,可根据具体的现场条件来选择上述三种模式之一,通常采用标准模式进行。
4.3 智能控制
(1) 零点迁移和自动跟踪
零点的迁移范围有两种:±2%MR和±5%MR。要实现零点自动跟踪,零点迁移范围必须选择±2%MR,系统自动记录称量斗内每次装入的净荷W1和卸出的净荷W2,然后计算差值ΔW, 根据ΔW的大小和极性自动修正称量装置零点。